Why VMC is the Best Way to Machine Heavy Parts
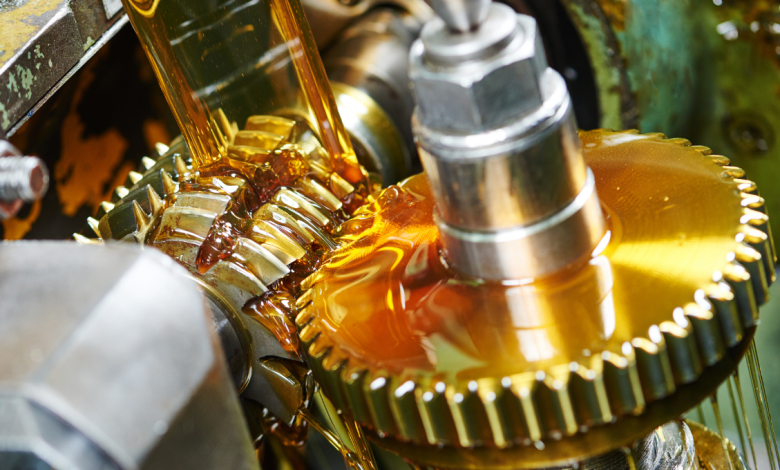
Machining heavy components can be incredibly difficult, especially if you’re going about it in the wrong way. That’s why vertical machining centers (VMCs) are so useful. Vertical machining centers (VMCs) are an innovative type of computer numerically controlled (CNC) machine tool that offers many benefits over older, more traditional horizontal machining centers, or even more modern CNC lathes.
VMCs are capable of much greater versatility than lathes and horizontal machining centers due to their versatility and range of motion. They provide several benefits to your business, and they can help you get the best results possible with your job work. Vertical machining centers (VMCs) are often the best choice when it comes to machining parts that are particularly heavy, awkward, or large. Let’s discuss how VMC machining job work is the best way to machine heavy parts :
- VMC machines can handle heavy workloads: VMC machines have many advantages over standard machining, including increased productivity and increased efficiency. One of the most popular machine types used in heavy machining jobs is a vertical machining center (VMC). A VMC machine can handle heavy workloads, which makes them ideal for projects that require high-volume production. Unlike horizontal machining centers, VMC machines can produce parts with complex geometries. The speed and power of these machines make it easier for companies to work on multiple jobs at a time.
- VMC machines are more precise: A vertical machining center (VMC) is a type of machine tool that has a spindle that moves in an up-and-down motion. The spindle is driven by lead screws, which are more precise than belt drives. This means that VMCs can be used for heavy jobs where belt drives would usually be used.
- VMC machines are faster: The speed of a VMC machine makes it ideal for machining heavy parts. Unlike traditional methods, you can use a CNC machine without having to slow down and make allowances for material removal. With a VMC, you can work at speeds that would be impossible with any other type of machine. VMC machines also have higher rates of production because they make fewer mistakes and require less setup time when compared with horizontal machining centers.
- VMC machines are easier to operate: When machining large, heavy parts, a vertical machining center (VMC) can be a better option than a horizontal machine. Traditional horizontal machining centers are less suited for these types of jobs because they’re typically designed for use on smaller workpieces that don’t require the same amount of rigidity or horsepower. Vertical machining centers can provide much more stability and power for these applications.
- VMC machines require less maintenance: The vertical machining center (VMC) is a type of machine tool that has been around for a long time. It’s used for turning and milling metal parts, and it saves time by allowing you to do both operations on one machine. It’s also more efficient than a lathe because its axis of rotation can be tilted in any direction. The downside of a VMC is that its milling spindle tends to require more maintenance than lathes because it operates at higher speeds. However, this doesn’t change the fact that it’s still the best way to machine heavy parts.
- VMC machines are more affordable than a lathe: A final reason why people prefer VMCs is that they cost much less than a lathe or turning center when set up properly. Lathes also use abrasives instead of cutting tools like turning centers, so they often need expensive consumables that wear out quickly and need constant replacement.